ElectriPlast: Business Profile
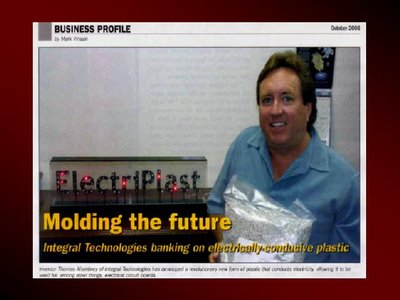
Molding
the
Future
By Mark Vinson
Northwest Business Monthly – Oct 2006
www.nwbusinessmonthly.com
[ElectriPlast Blog Publisher's Note: This article appears in the "print only" portion of this monthly magazine. I have a copy of the article on hand in PDF format, and will happily forward to any asking. Email me at: electriplast@hotmail.com -- PK sends...]
Integral Technologies Banking on Electrically Conductive Plastic
Inventor Thomas Aisenbrey of Integral Technologies has developed a revolutionary new form of plastic that conducts electricity, allowing it to be used for, among other things, electrical circuit boards.
It’s quite possible that the future of the electronics industry is being molded in an obscure Bellingham laboratory, where plastic is replacing metal as the material of choice for everything from circuit boards to cell phone antennas to wire cable itself.
We're talking something here that can be as big or bigger than Microsoft...
For the past five years, Thomas Aisenbrey of Integral Technologies, Inc. has been developing and perfecting a revolutionary, patented material called ElectriPlast, which can do everything copper and aluminum can in a lighter, cheaper manner. “We're talking something here that can be as big or bigger than Microsoft” said Aisenbrey, a 48-year-old inventor who fell in love with all things scientific as a child – built his first radio as age eight and hasn’t stopped discovering new technologies since.
Anything you can make out of metal, we can make out of plastic now
Aisenbrey came to Bellingham from Colorado in 2001 to work for Integral, building flat antennas for trucks. Shortly thereafter, he realized that a new form of electronically conductive plastic could eventually make wire antennas obsolete. “Anything you can make out of metal, we can make out of plastic now,” he said.
The advantage is that plastic is lighter, stronger and far easier to mold and shape, thus making the manufacturing process less expensive. ElectriPlast which is 40 percent lighter than aluminum and 80 percent lighter than copper, can be used to make antennas, wiring, heating coils, circuit boards, braking systems for vehicles, burners for boats, in pacemakers and other medical devices and much more. In the case of a cell phone, for example, the casing itself can be made from ElectriPlast and double as the antenna, replacing the wire antenna that protrudes from most phones today and improving signal reception.
ElectriPlast “has all the properties of plastic, yet has the ability to conduct electricity,” said Aisenbrey, Integral’s chief technology officer and general manager. “Plastics have changed the world and now ElectriPlast is changing the world of plastics.”
I think 2007 is our breakout year
Or it may someday soon. There aren’t yet any products on the market using ElectriPlast. “I think 2007 is our breakout year,” said Integral CEO Bill Robinson of Vancouver, British Columbia.
The company has recently entered licensing agreements with Heatron, a heating and LED company based in Kansas City, MO., and with Jasper Rubber Products of Jasper, IN. Robinson expects more agreements to be signed by the end of the year.
“We’re licensing the technology to different companies,” said Aisenbrey, adding that Integral has no plans to manufacture products itself.
Integral packages its recipe for ElectriPlast in the form of tiny pellets smaller than a thumbtack. These pellets, which will be mass produced at a warehouse in the Midwest, are packaged, sold and shipped to manufacturers who then pour them into molds to make whatever product is desired.
“There are more than 15,000 different resins we can put our recipe into,” Robinson said.
Integral markets ElectriPlast at trade shows and has been featured in Popular Science magazine. Ironically, the entire concept of ElectriPlast is so revolutionary to some that it has required time to gain widespread acceptance in the marketplace.
“A lot of people aren’t molders out there,” Aisenbrey said. “You have engineers that know nothing about plastics, nothing about molding. There are some hurdles out there that you have to overcome. We’re working now with the molders of the world, not the electronic guys. The electronic guys shy away from something they don’t know anything about.”
The publicly traded company reported a net loss of $459,000 for the second quarter of 2006 and more than $20 million since it’s founding in 1996. But those figures aren’t surprising to Robinson and co-founder Bill Ince of Bellingham.
“We’re a research and development company,” Robinson said. “The reality is, it takes from five to seven years once you have a handle on your product.”
Integral received a $6 million investment from the Wellington Investment Group of Boston in 2004, which “allowed us to write our full patent portfolio,” Robinson said. Integral has 18 patents on file and applications for nearly 100 more pending, each covering a specific use of ElectriPlast.
Robinson, who has successfully managed and later sold other companies in the past, won’t rule out the possibility of selling Integral someday if ElectriPlast becomes the latest industry revolution.
“I think this is one of the biggest things you’ll see transforming manufacturing in our lifetime,” Aisenbrey said…
0 Comments:
Post a Comment
<< Home