ElectriPlast -- Developing Plastic Batteries…
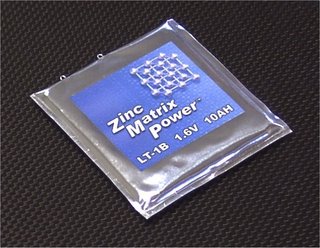
The following is a Research and Development missive, speaking to the emerging Plastic Battery technology.
Recent lab tests indicate that rechargeable Plastic Batteries can potentially double the capacity and volume of use over that of today’s Lithium-based batteries.
How does Integral Technologies and their Intellectual Property material, ElectriPlast, fit into the equation? Moreover how can this fact be of benefit to you or I as prospective marketplace consumers, or (if you happen to be one) as an Integral Technologies, OTCBB: ITKG shareholder?
There are simple answers to these questions…
First though, to describe the concept of a Plastic Battery.

According to the Integral Technologies patent information, submitted by Tom Aisenbrey -- ElectriPlast could end up playing a significant role by providing a key component in a revolutionary new type of battery that will soon become available commercially. Unlike the standard of today, this revolutionary battery will store its electricity in plastic.
Environmentally Friendly…
A Rechargeable Plastic Battery is first and foremost considered environmentally friendly. Plastic batteries are the most radical innovation in commercial batteries since the dry cell was introduced in 1890. Unlike metal-based nickel-cadmium rechargeable batteries, plastic batteries contain no heavy metal, which can contaminate soil and water. Plastic batteries also contain no liquids, which can leak and pose safety hazards.
The Many Positives…
The Plastic Battery operates efficiently in extreme heat or cold; whereas the reliability and properties in a number of other type battery materials vary with temperature—for example, today’s standard car battery does not always start well when exposed to extreme cold.
Plastic Batteries also offer higher capacity, higher voltage, and longer shelf life than many competitive designs. According to Integral Technologies Investor Relations, a number of companies are using these plastic batteries to test new shapes and configurations, including flat batteries, which are credit card thin, and can be bent like cardboard, or cut and folded into a specific shape.
Design Flexibility…
Plastic batteries are extremely light weight—in fact, depending on the process used to create these batteries, they can be anywhere between 60-90% lighter than that of conventional metal batteries. (Consider this as a comparison -- imagine that time you changed out the battery from your car. This battery weighed anywhere from 25 to 50 lbs. Most of that weight was due to the lead plates within the battery, and the conductive fluid 'acid'. In using a plastic battery, the future weight of the car battery will be anywhere from 8 to 22 lbs, and without the hazard of conductive fluid sloshing about within. Consider further the impact that such a change could make on both the electric car and hybrid vehicle industries.) These batteries have the capability of being molded into almost any size and shape—this factor in itself has implied military and space applications. The flexibility in this technology is a key factor that will one day free electronic designers from many of the constraints (such as limited recharging cycles, high weight & high cost) presently imposed by the use of metal batteries.
Imagine if you will, using a battery in a large sheet form, so that you could have a battery that occupied an entire wall for example, while keeping in mind that it had very little thickness. With that in mind, the uses and applications in this form become limitless.
Less Internal Wear & Tear…
Chemically, the plastic battery is different from conventional metal-based rechargeable batteries. In metal-based batteries, material from one plate migrates to another plate and back in a reversible chemical reaction. In a conducting plastic battery, the anode and cathode are made of thin, non-degrading, foil-like plastic sheets. The electrolyte is a polymer gel film placed between the electrodes holding the battery together. In short, unlike the conventional battery with its chemical reaction there is no metal plate being constantly consumed, a factor which severely limits the number of times the battery can be recharged/reconstituted. In other words, a conventional battery life is limited by the number of times the plates can be reconstituted. This difference portends to a longer recharge-cycle lifetime for the plastic batteries.
Other Benefits of Developing a Plastic Battery:
In addition, with a growing energy need on the consumer front, plastic batteries (from a manufacturing standpoint) are very easy to make, using simple stuff—organic compounds. They easily lend their superior applications to suitable consumer devices—from solar cell charging systems, car batteries, laptops and cell phones to smaller items such as hearing aids and wristwatches.
Reference Material:
- http://www.zmp.com/news.html New Battery Technology in Development to potentially double laptop run times. 9 June 2004
- http://www.jhu.edu/news_info/news/home96/nov96/batt.html Power from Plastics: Hopkins Scientists Create All-polymer Battery. 12 Nov 1996
- http://www.osti.gov/accomplishments/macdiarmid.html Alan MacDiarmid, Conductive Polymers, and Plastic Batteries.